The Different Parts of a Continuous Pyrolysis Plant
Continuous pyrolysis plants are a new technology that is being used to convert biomass into biofuels. This type of plant has several different parts that work together to create a sustainable and efficient renewable energy source. In this blog post, you’ll learn about the different parts of a continuous pyrolysis plant and how they function.
How Does a Continuous Pyrolysis Plant Work
A continuous pyrolysis plant is a facility that thermally decomposes biomass in the absence of oxygen to produce biofuels and other useful products. The process of pyrolysis is used to break down organic materials, such as wood, into their smaller chemical constituents. This process can be used to generate a variety of renewable energy sources, including electricity, transportation fuels, and heat.
This type of plant differs from other pyrolysis plants in that it uses a continuous feed of biomass instead of batch processing. This allows for a more efficient process and less waste overall. There are three main parts to a continuous pyrolysis plant: the reactor, the condenser, and the gasifier.
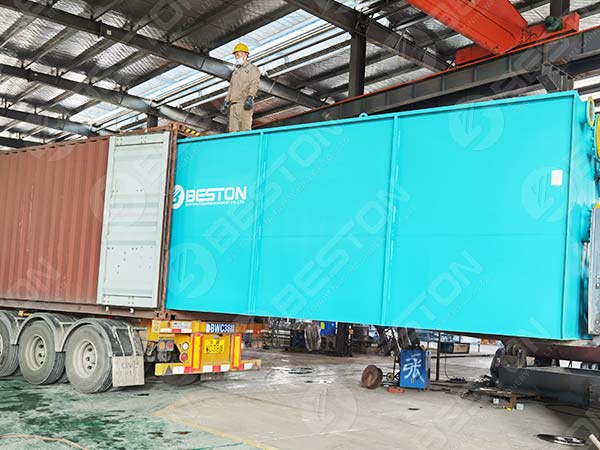
Continuous Pyrolysis Plant Is Ready to Ship
The Reactor
The reactor is the heart of the continuous pyrolysis plant, where the biomass is converted into biofuels. There are two types of reactors that can be used in this process: the rotary kiln and the fluidized bed.
The rotary kiln is the most common type of reactor used in this type of plant. It consists of a large cylinder that is rotated to evenly distribute the biomass. As the biomass is heated, it breaks down into smaller molecules that are then condensed into a liquid.
The fluidized bed is another type of reactor that can be used. In this type of reactor, the biomass is suspended in a bed of air or steam. As it is heated, the biomass breaks down into smaller molecules and is condensed into a liquid. More information on tire pyrolysis plant here.
The Condenser
The condenser is used to cool the biofuels that are produced in the reactor. This is necessary to prevent the biofuels from evaporating. There are two types of condensers used in a continuous pyrolysis plant: the air-cooled and the water-cooled.
The air-cooled condenser is the most common type of condenser used. It consists of a large fan that blows air over the biofuels to cool them.
The water-cooled condenser is less common, but it is more efficient. It uses water to cool the biofuels instead of air.
The Gasifier
The gasifier is used to produce methane, which is a major component of natural gas. The gasifier works by breaking down the biomass into smaller molecules. These molecules are then condensed into a gas. The methane is then used to power the plant. Check the pyrolysis plant for sale here.
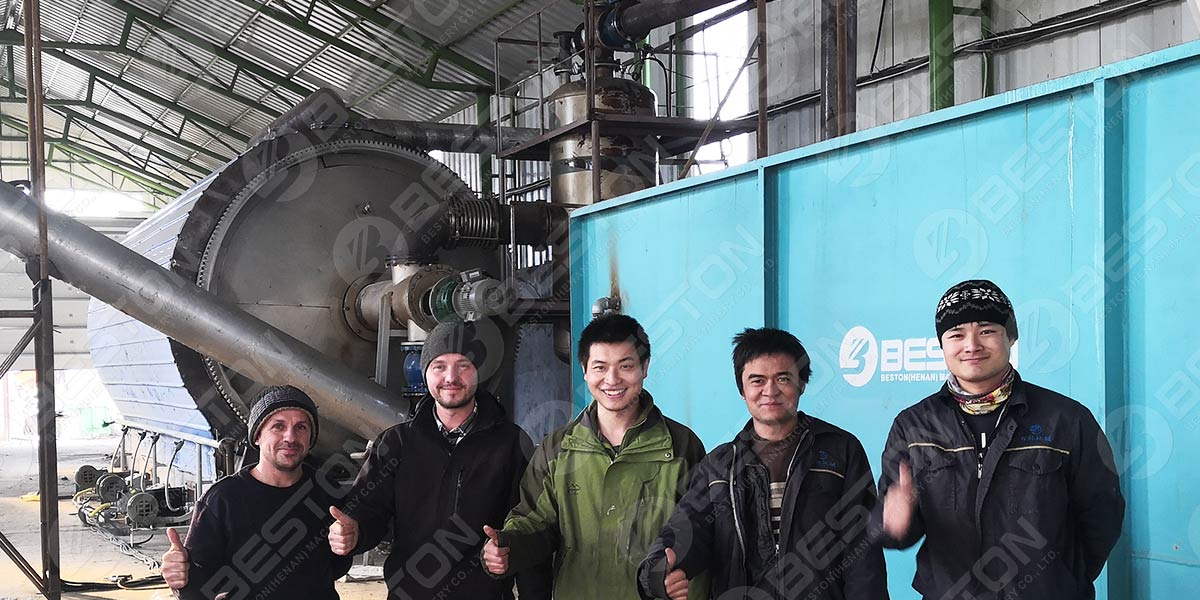
Continuous Pyrolysis Plant in Romania
Benefits Of Using a Continuous Pyrolysis Plant
There are several benefits to using a continuous pyrolysis plant over other types of plants.
The first benefit is that it is more efficient. Continuous pyrolysis plants use less energy overall to produce the same amount of biofuels as batch processing plants. Over time, this can lead to significant cost savings.
The second benefit is that it produces less waste. Continuous pyrolysis plants produce a solid, liquid, and gas waste product. The solid and liquid waste can be used as a fertilizers or as animal feed. The gas waste can be used to power the plant.
This type of plant is more scalable as well. Continuous pyrolysis plants can be easily scaled up or down to meet the needs of the customer.
Lastly, it is easier to operate. Continuous pyrolysis plants are less complex overall and require less operator training. Get pyrolysis plant cost here.
- Buying A Biomass Carbonization Machine
- The Rise in Popularity of the Mobile Biochar Machine